Deployment of the autonomous truck-mounted attenuator (ATMA) in Florida has the potential to significantly increase worker safety and save taxpayer costs during highway maintenance and construction. The evaluation will identify strengths and limitations and conduct a cost-benefit analysis of the ATMA to evaluate its usefulness for improving worker safety of Florida highways. Before introducing the ATMA technology to Florida roadways, the research team will use a controlled testing environment with no traffic to assess safety features. UF researchers will also examine use of the ATMA technology in real work zones on different roadway types, including high speed urban and rural roadways and low speed urban roadways. The ATMA will follow and protect a work vehicle which will be equipped with a falling weight deflectometer (FWD), a device which evaluates the strength of pavement.
Overview of ATMA Technology
The ATMA system removes workers from a very dangerous job: driving a slow moving vehicle to protect or shield a work vehicle. These vehicles operate on roadways with varying traffic volumes and speed, including high speed interstate highways. Emergency roadway repairs or planned maintenance activities often require a TMA to absorb the impact of a vehicle that mistakenly enters a work zone. Despite the attenuator, a TMA driver can still suffer serious injury or be killed in this situation. The ATMA does not require a driver, eliminating these hazards.
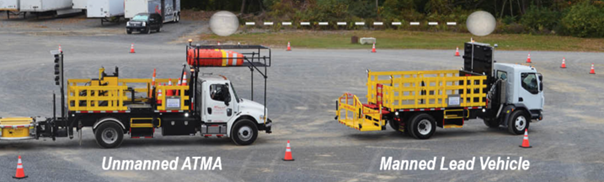
The ATMA is operated in a leader-follower configuration in which the human-driven work vehicle is followed by the unmanned ATMA. Standard vehicles are retrofitted with technology that enables unmanned operation, including navigation, communications system, an operator control unit with a kill switch, a tablet computer, a rear- and forward-facing video cameras, actuators for controlling steering, braking, and acceleration, sensors for obstacle detection, and external kill switches on the ATMA and an independent remote kill switch.
An advantage of the ATMA system is that it offers a solution that does not require any infrastructure improvements. It relies solely on GPS and real-time kinematic (RTK) positioning technologies.
Potential Benefits of ATMA Technology
The UFTI-T2 Center is excited to explore the potential benefits of the ATMA deployment, including increased safety for workers, cost reductions, and safer and more efficient work zones. Several ATMA benefits will be explored during the evaluation:
- MUTCD guidance: The ATMA is able to maintain a highly accurate gap between leader and follower vehicles, which is difficult for a human driver and sometimes endangers workers in the lead vehicle when the TMA is too close.
- TMA driver: A driver is no longer at risk of injury or death from a rear-end collision with autonomous leader-follower technology.
- Maintenance crew: In the event of a potential collision, a TMA driver may instinctively get out of the way instead of maintaining a protective position, putting a work crew at serious risk. The ATMA will never veer out of the way to avoid an impact.
- Crash costs: Claims associated with serious injuries and death from work zone incidents cost millions of dollars. The ATMA could reduce the cost of these claims.
- Autonomous technology: The ATMA provides a significant amount of data that is useful for planning and deployment of future connected or autonomous vehicles.
System Performance Evaluation
The UFTI-T2 Center will evaluate the ATMA follower and leader vehicles in controlled testing environments and assess the system’s ability to detect obstacles, interferences, and intrusions between the leader and follower. TMA operators will have the opportunity to participate in demonstration, training, and trial sessions.
On-site field testing will follow the controlled sessions to provide a comprehensive range of data for analysis. During closed-loop testing and work zone deployments, UFTI-T2 will focus on ATMA features, including system redundancy, geometric design limitations, offset ability, lane shifts to shoulder and back to travel lane, signal timing, and intersection distance considerations. Field-testing sites include:
- Controlled pre-test environment with no-traffic
- Multilane rural or semi-urban high speed environment with low traffic volume
- Interstate high speed environment with high traffic volume
- Urban low speed environment with signalized intersections, side streets, and high traffic
- Rural or semi-urban two-lane roadway
Before, during, and after the ATMA equipment testing and operation, UFTI-T2 Center will document qualitative and quantitative feedback from study participants to integrate the user experience into the evaluation.
Stay tuned as we report the findings of the demonstration and evaluation study in our next newsletter! For more information on this study, please contact Dr. Nithin Agarwal at nithin.agarwal@ufl.edu.